Share this
10 Tools That Every Mechanical Engineer Should Know
by Career Guide on Jul 17, 2023 9:00:00 AM
Mechanical engineers need to know how work with a variety of tools and programs to succeed. Here are ten of them.
By Mark Crawford
Mechanical engineers draw upon a wide range of disciplines for their projects, including mathematics, engineering, physics, materials science, and chemistry. Engineers use a variety of tools that make their jobs easier and more efficient, resulting in higher-quality products and faster production. As manufacturing technologies advance, especially with the challenges of smaller parts and tighter tolerances, it is more important than ever to have handheld and digital tools that provide the speed and high precision that mechanical engineers require.
Here are ten essential tools that most mechanical engineers cannot do without.
1. Fiber laser machines
A fiber laser machine is essentially an engraver that uses a laser to mark metal surfaces such as anodized aluminum, zinc, and steel. Markings range from engraving serial numbers on parts to logos, QR codes, and barcodes. Depending on production needs, models range from manually loaded machines to fully-automated systems that utilize robotic arms for loading and holding parts.
2. Vibration isolator
Vibration is often a problem with equipment because it can damage components and impair performance. Engineers rely on vibration isolators to detect and measure vibrations in machinery. Springs are typically used as the isolators to minimize force and may include fluid damping, steel coil, pneumatic, and rubber components. Mechanical engineers can then quickly isolate the cause of the vibration and fix it to restore smooth operation.
3. Coordinate measuring machines
Coordinate measuring machines (CMM) are computerized measuring devices that take extremely precise measurements. CMMs are ideal for parts and components that require extreme dimensional control and automatically measure parts to ensure they are within tolerance. This equipment can be inline or offline and can measure features as small one micron in diameter.
4. Cold forming press
Cold forming is a high-speed, room-temperature forging process that cuts wire and pushes it through a succession of tool and die cavities to turn it into the required shape for the product being made. The metal is forced beyond its yield (elastic) limit but not beyond its tensile strength, which would result in fracture. Cold forming can process metal, plastic, and other materials; new machines on the market are equipped with more digital features.
5. 3D printer
Mechanical engineers use 3D printers to make solid, plastic or metal parts for their designs that are tested as prototypes (function, strength, material properties) or fabricate replacement parts for equipment or jigs and part-holders. 3D printing enhances prototype development by saving time, improving design, reducing iterations, and optimizing inventory. Top software programs for 3D printers include Fusion 360, Solid Edge, Tinkercad, and OnShape.
6. Digital force gauge
Also called a push-pull force gauge, a digital force gauge has a load cell inside that measures the amount of tension or pressure for a part or component in a machine. Engineers use these gauges when building and testing equipment, including critical components such as wiring, to be sure all parts have the proper tension. These gauges are available in digital, analog, and mechanical styles.
7. Calipers
A caliper is a common but highly valuable tool. Similar to a drafting compass, it is used to measure a product’s dimensions, including internal parts and components, with a high degree of accuracy. Far more accurate than a ruler, calipers provide all the dimensions for a part or product so that it can be recreated with precision. Many engineers prefer digital vernier calipers, which are highly accurate with a tolerance of about 0.01mm.
8. FEA software
Finite element analysis (FEA) helps engineers determine how a product will react to real-world stresses such as temperature, air flow, fluid flow, impact, and vibration. These simulations are invaluable for undertaking structural analysis on stresses and deflections in complex structures and testing for probable points of failure. Popular FEA software programs include ANSYS and Autodesk Inventor.
9. Visual Basic for Applications (VBA)
Visual basic is a coding program that mechanical engineers use to automate many of their digital tasks. Visual basic can be paired with Excel to automate calculations and other functions. VBA is easily customized to create user-defined functions such as analyzing big data and generating complex financial models; when paired with CAD software, VBA improves efficiency by automating computer processes and repetitive functions.
10. MATLAB (Matrix Laboratory)
MATLAB is a programming language or environment developed by MathWorks. Engineers use this program for modeling, design, prototyping, and data analytics. MATLAB enables matrix manipulations, plotting functions and data, implementation of algorithms, creation of user interfaces, and interfacing with programs written in other languages. Its plotting capability allows for easy simulation and fast display of results.
With the rapid development of advanced manufacturing technologies and related software, the tools that mechanical engineers have grown to trust will gradually go out of date as digital, next-generation tools take the stage. Becoming experts with these analytical tools will help MEs become more efficient, design higher-quality products, and be tool-proficient when Industry 4.0 hits full stride.
Mark Crawford is a science and technology writer in Corrales, N.M.
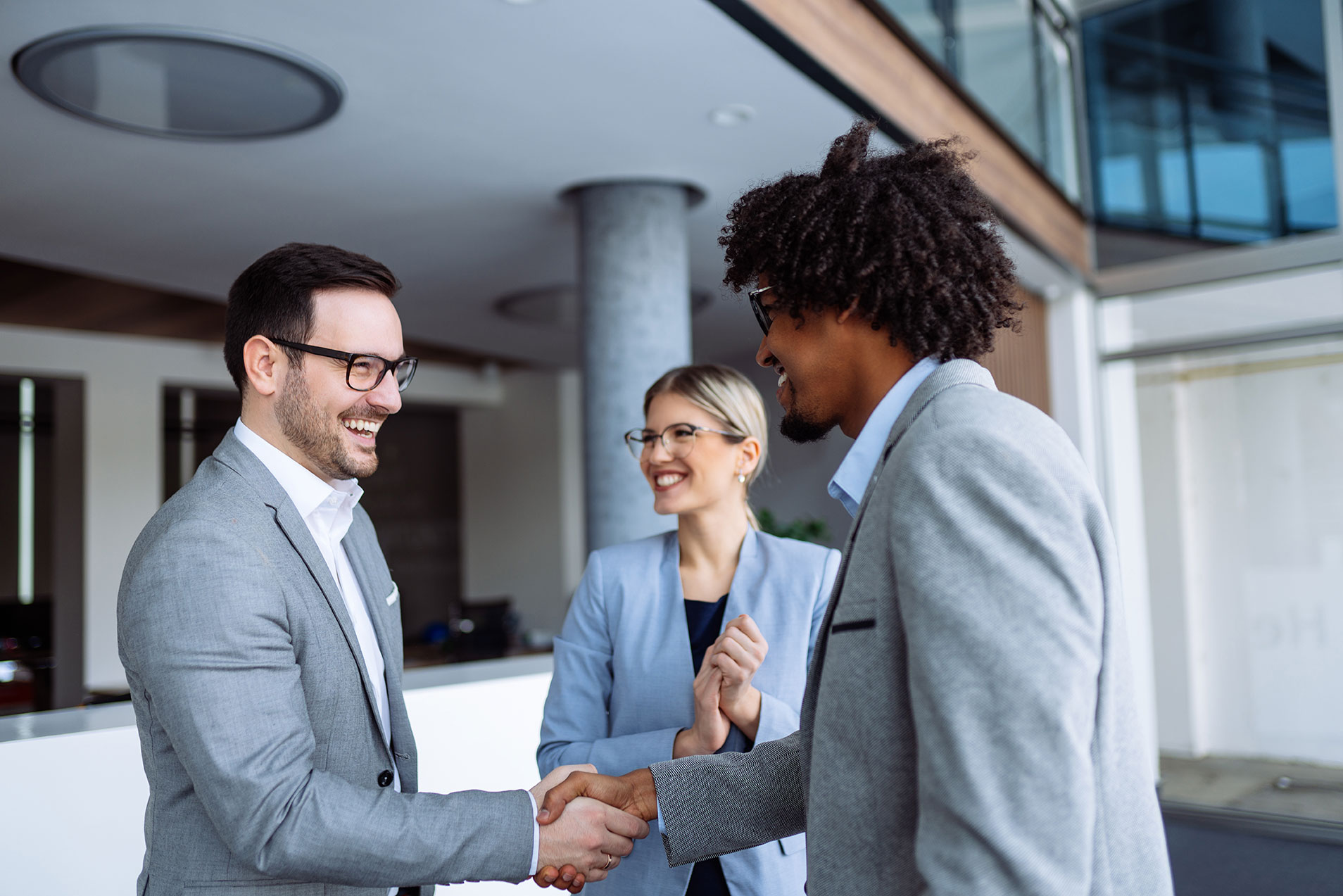
10 Networking Mistakes That Make You Look Unprofessional
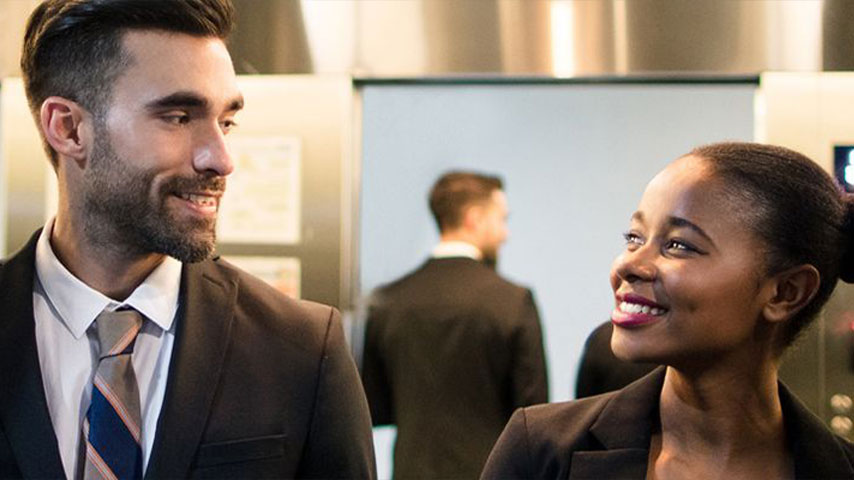